The application, the size and number of loads to be managed, the necessity for monitoring and reprogramming the circuit, and the amount of control necessary (ON/OFF to anywhere in between) all influence the type of programmable logic controller (PLC) that is utilized.
Budget costs and the personnel’s level of expertise in terms of programming the circuit/system, maintaining the system, and updating it must also be taken into account.
The demand for more exact programming, control, flexibility, and monitoring increases as a system gets bigger and more sophisticated.
Programmable logic controllers (PLCs), programmable logic relays (PLRs), and programmable automation controllers are examples of programmable controller types (PACs).
What is Programmable Logic Controllers (PLCs)
A programmable logic controller (PLC) is a solid-state control device that is designed to be programmed and reprogrammed to automatically control industrial processes or machine circuits.
Although practically any sort of electrical control circuit can be controlled by PLCs, these devices were primarily created for the more abrasive conditions prevalent in industrial applications. Look at Figure 1. The central processing unit (CPU), the power supply, the input portion, and the output section make up a PLC.
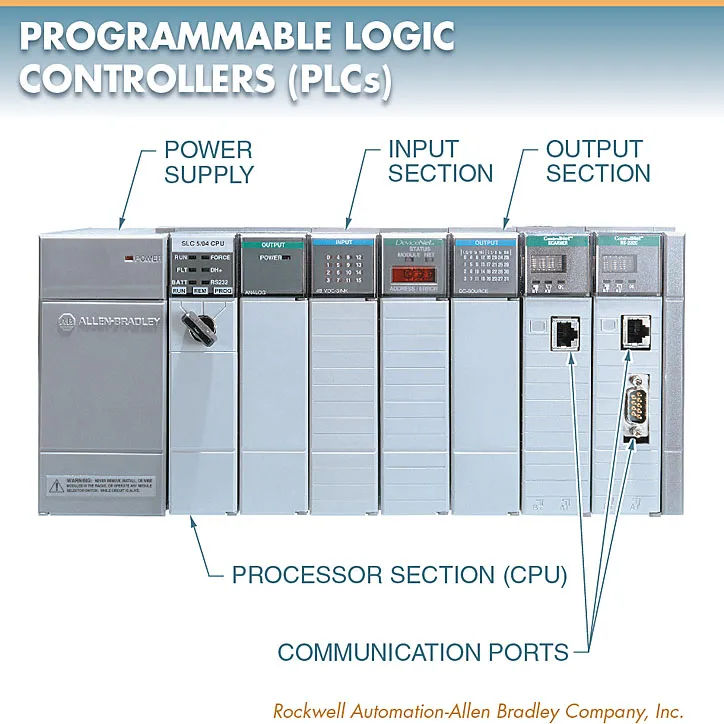
With the help of various input and output (I/O) modules that can connect to 3, 11, 32, or 14 devices, PLCs can control circuits with numerous inputs and outputs.
Within a rack, individual modules may be added and arranged in groups of four, one, three, twelve, or more. There, I/O capabilities can be increased by adding extra expansion modules and/or linking many PLCs into a single control system, enabling the control of applications with more than 1000 I/Os.
The essential components of smaller PLCs, also known as stand-alone PLCs, are identical to those of bigger PLCs, however they cannot be exchanged or expanded with new modules. They can be combined to create larger systems, or a “extension” module can occasionally be added, but they are made to run smaller circuits with the maximum amount of available I/O.
The majority of PLCs are made to be programmed using function blocks or line (ladder) programming. Utilizing software created by the manufacturer specifically for the type of PLC in use, programming is carried out. The size and complexity of the PLC determine how sophisticated the programs are, but all programs use the same programming tools (inputs, outputs, timers, counters, etc.) and operating features (circuit monitoring, I/O forcing, etc.).
Programmable Logic Relays (PLRs)
A programmable logic relay (PLR) is a solid-state control device that includes internal relays, timers, counters, and other control functions that can be programmed and reprogrammed to automatically control small residential, commercial, and industrial circuits.
PLRs are essentially miniature PLCs created for more generic control applications with fewer inputs (often less than 10) and outputs (usually less than 1). Some manufacturers refer to PLRs as “smart relays” or list them as “nano” or “micro” PLCs because they are essentially little PLCs. Whatever the manufacturers choose to call them, these PLCs can be programmed and used in the same ways as small circuit PLCs. Look at Figure 2.
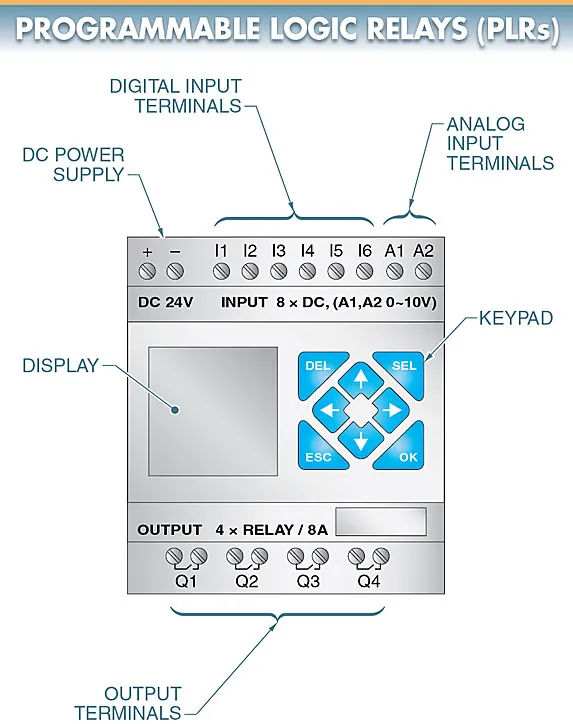
PLRs can be programmed using line (ladder) programming or function blocks, just like PLCs. Because the local viewing window is limited and can only show a portion of the broader program, programming and circuit monitoring are best carried out by connecting the PLR to a PC, even though they can be programmed using only the provided keys and display.
The local display and operating keys are useful for viewing/changing operational features including run or stop modes as well as programming passwords and languages into the device (though the device will often offer several common languages).
Programmable Automation Controllers (PACs)
A programmable automation controller (PAC) is a combination of a PLC and a PC-based CPU control device that is designed to operate in an industrial environment.
To autonomously control a big industrial process, PACs can be programmed and reprogrammed using typical PLC languages (ladder or function blocks) or PC languages (structured text, sequence function charts, etc.).
The operating system for the entire PAC is made up of a number of interconnected components, including human-machine interfaces (HMIs), remote monitors, data acquisition, motion control, and vision control devices.
Like PLCs, PACs are made to function in the challenging conditions present in industrial applications. Self-contained PACs are available and include the power supply, CPU, and input or output components made for specific control functions. Additionally, they can be found in rack-mounted devices that can be combined to operate large systems. Look at Figure 3.
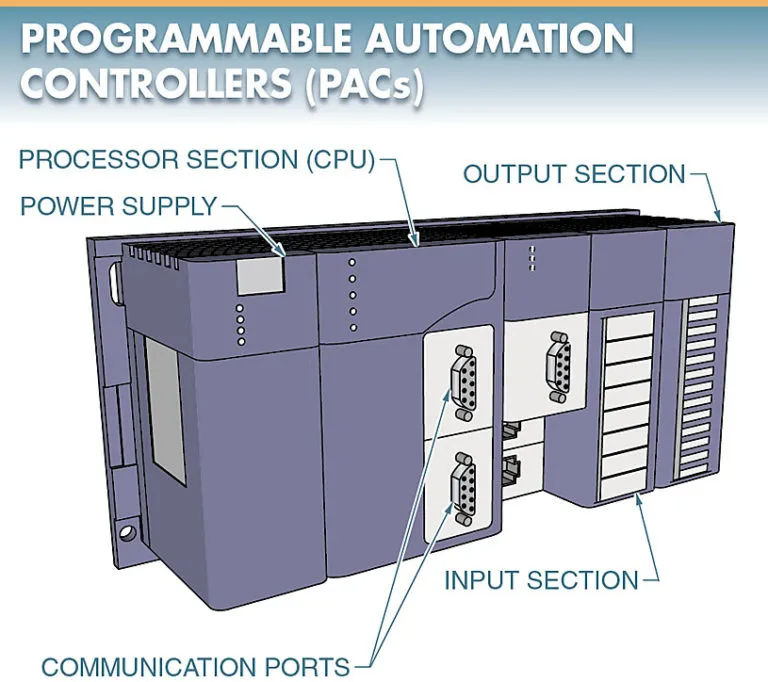
Similar to PLC units, PAC units may have fundamental I/O modules, such as temperature and digital or analog I/O modules. Additionally, specialist modules for servo/stepper motor control, serial connection, and data collecting may be present in PAC units.
For use with control inputs such thermocouples, resistance temperature detectors (RTDs), pressure monitors, flow monitors, distance detectors, strain gauges, and other analog output devices, process voltage (0 VDC to 10 VDC) and current (4 mA to 20 mA) analog control modules are also offered.
Programmable Controller Selection
A PLC is typically regarded as the best option for managing industrial electrical systems and circuits. When a system doesn’t need many internal controller timers, counters, or loads (outputs) or control switches (inputs), a PLR may be an option.
Similar to a big process control system, a PAC can be taken into account when more advanced control is needed to operate within a huge system and PC-based network.
A PLR can be utilized when a PLC is being considered, as long as the control circuit is small enough and won’t be operating in an unforgiving industrial environment. If the control system also needs vision control, servo/stepper motor control, motion control, HMI, data acquisition of process conditions, and/or servo/stepper motor control, a PAC can be employed.
PLCs, PLRs, and PACs are becoming more and more common, functional, quick, and able to connect into various networking systems to allow individual components and units to communicate with one another.
The same fundamental control needs apply to PLCs, PLRs, and PACs, which include the following:
- adjusting circuit outputs dependent on the state of the circuit.
- its input portion is connected to digital (OPEN/CLOSED) inputs.
- linked to their input portion are analog (infinite position) inputs.
- digital outputs with output section control (ON/OFF).
- Controlled by their output portion are analog outputs with indefinite working conditions.
- a method or approaches for using computers to program the control circuit.
- a PC with circuit monitoring software, printing manuals, and system/component troubleshooting tools.
- extendable and connectable to create bigger systems
Programmable Controller Configurations
Programmable controllers can be integrated into a system or used as standalone control devices. A programmable controller can be set up in a system that makes use of a personal computer, a portable programming device, an operator interface panel, additional programmable controllers, or other electrically connected devices.
The operating requirements and cost of the system determine the degree and amount of control between the components in a programmable controller.
The configuration of a programmable controller’s system is determined by the type and quantity of required I/O devices, required communication between devices, programming types and requirements, and any future needs. See Figure 4.
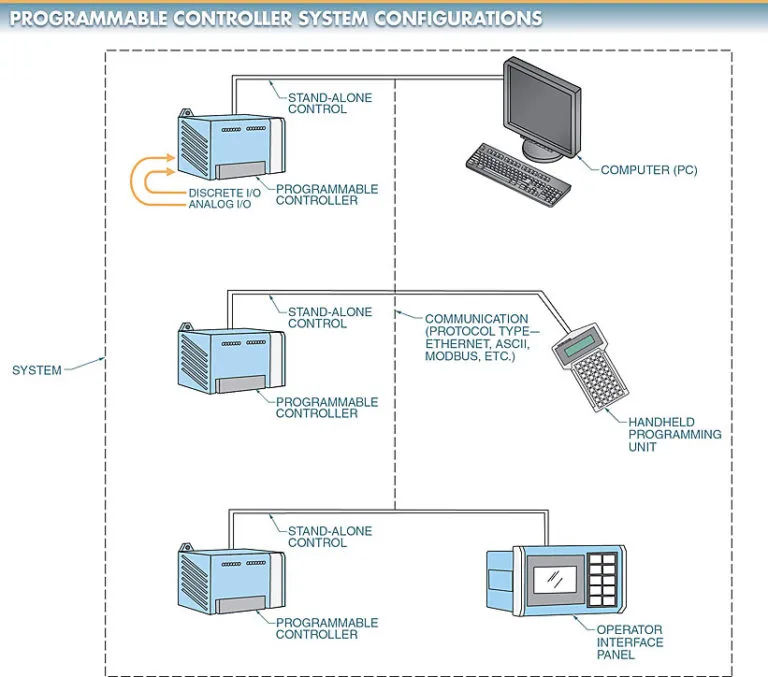
Figure 4 shows how the kind and number of necessary I/O devices, the quantity of necessary communication between devices, the types and requirements for programming, and any potential future demands all affect how a programmable controller system is configured.