In different situations, transformers can have different connections. Single-phase and three-phase connections can be made. A three-phase connection is more common in commercial and industrial settings, while a single-phase connection is more common in homes.
The windings of high-voltage transformers are labeled “H1, H2, etc.,” while those of low-voltage transformers are labeled “X1, X2, etc.”
Single-Phase Transformer Connections
Lighting, heating, cooling, cooking, and other household activities all rely on electricity, and this is true for both single- and multi-family homes. The standard 1, 120/240 V service is provided to homes.
The low voltage (120 V) is used for general-purpose receptacles and general lighting. The high voltage (240 V) is used for heating, cooling, cooking, etc.
Both overhead and lateral systems are available for supplying electricity to homes. The term “overhead service” refers to a type of electrical service in which the service-entrance conductors are suspended in the air from a utility pole and connected directly to the building.
A service lateral is a type of electrical service in which the service entrance conductors are laid below ground from the utility pole to the service location. For an example, see Fig. 1.
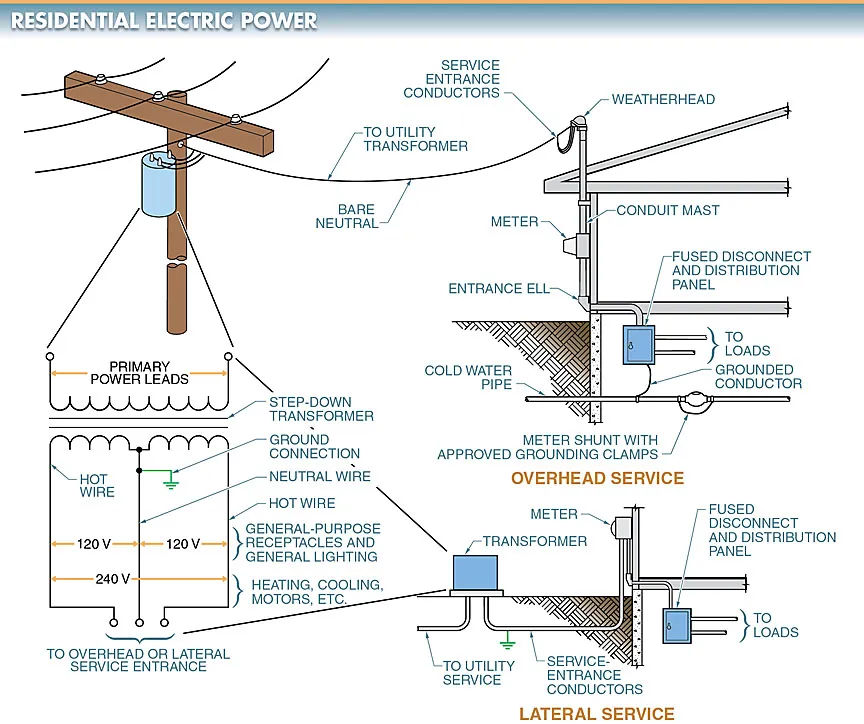
Three-Phase Transformer Connections
Connecting three 1 transformers together creates 3 voltage. In either a wye or delta configuration, the three transformers will work.
Each coil’s end in a wye connection is either hardwired to the primary power lines coming into the building, or is used to power the building’s load or loads (secondary side). The coils are joined at their opposite ends.
Each transformer coil in a delta connection is joined to the next to create a closed loop. Each node in a delta connection is either hardwired to the power source or directly connected to the load(s) it serves.
Whether the transformer is wired in a wye or delta configuration determines the voltage output and the type of voltage available to the load or loads. Check out the diagram in Figure 2.
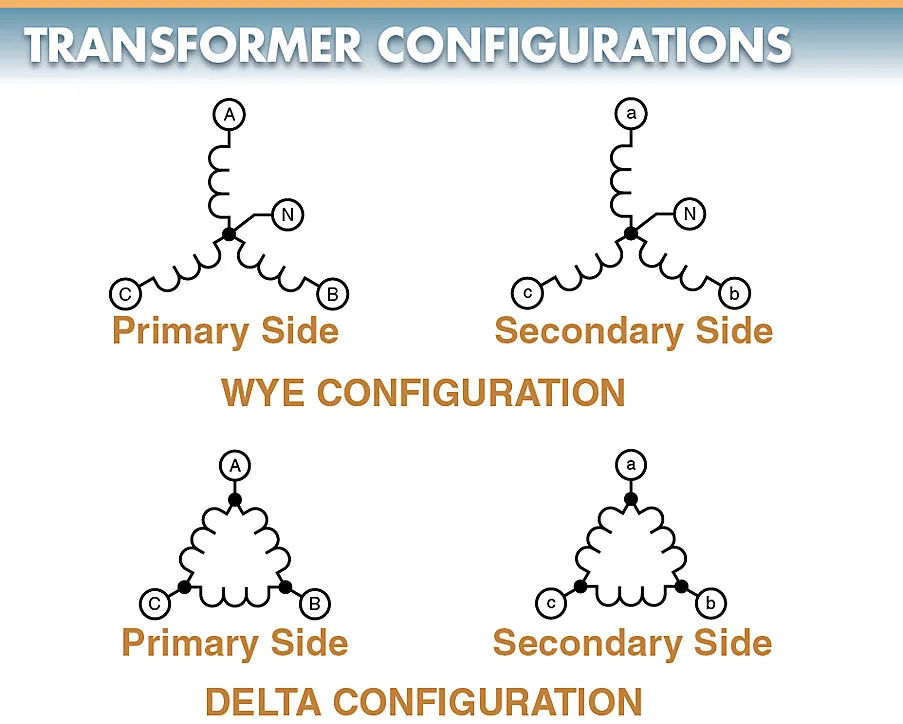
Transformer Secondary Taps
An additional lead (tap) is connected to the secondary coil of many transformers.
A tap is a connection brought out of a winding at a point between its endpoints to allow the voltage or current ratio to be changed. Taps allow different output voltages to be obtained from a transformer. See Figure 3.
When the turns ratio is 1:1, the voltage between leads 1 and 2 is 120 VAC, as an illustration (100 to 100). The turns ratio is roughly 4.17:1, which results in 24 VAC between the tap and lead 1. (100 to 24).
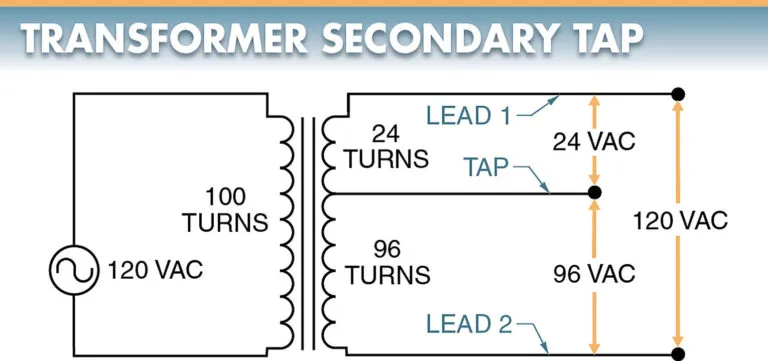
A center tap is a tap placed in the middle of a secondary to create two equal halves. A center-tapped transformer is typically used as a distribution transformer.
To convert the high voltage from the power company’s distribution lines to the standard 240/120 VAC supply used in homes and businesses, a distribution transformer is installed. Look at Figure 4.
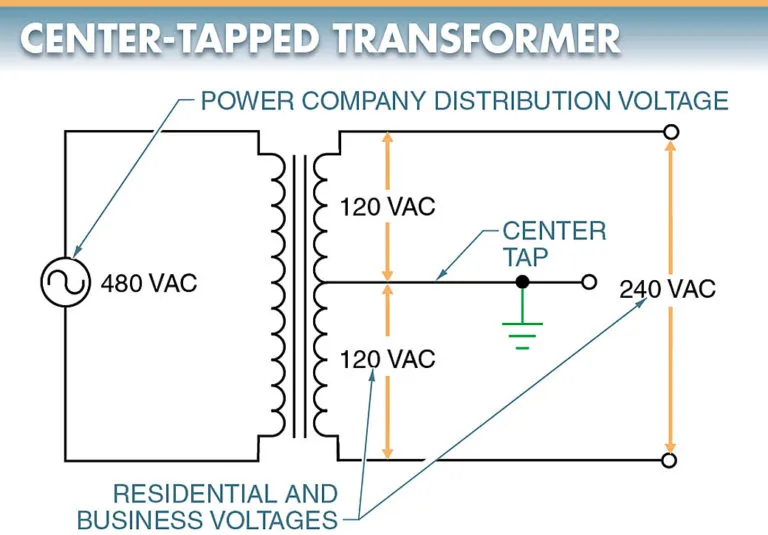
The center tap is connected to earth ground and becomes a common conductor. This system has a 240 VAC output voltage. However, the voltage measured between either output line and the center tap is 120 VAC.
The 240 VAC power is used to supply devices in the residence that require a large amount of operating power, such as a central air conditioner, water heater, clothes dryer, and cooking range. These high-power devices run on 240 VAC to allow smaller conductor wires to deliver power to them.
The 120 VAC power is wired to the electrical outlets and lighting system. This results in a significantly lower voltage, which is ideal for use with more delicate electronic equipment.
Control Transformers
A control transformer is a type of transformer used to reduce the input voltage to a device’s or system’s control circuit. Common control transformers use a design with two primary coils and a single secondary coil. Take a look at 5 below.
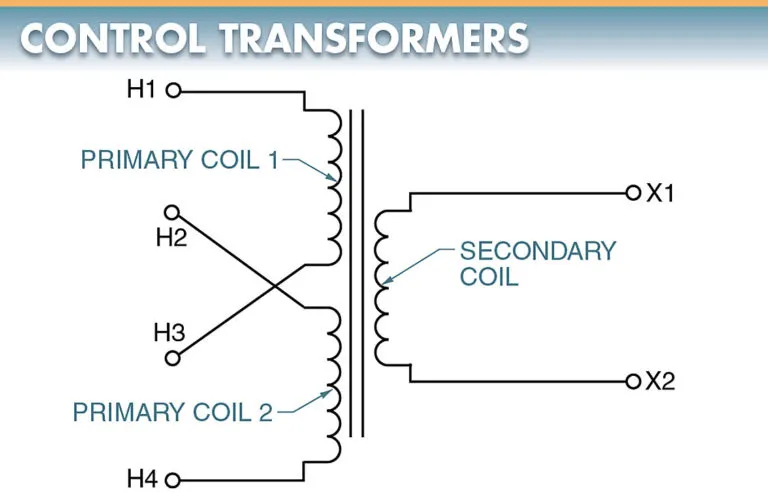
For use with either 240 VAC or 480 VAC, the primary coils of a control transformer are crossed and connected via metal links.
In most applications, a control transformer is used to reduce the main or line voltage of 240 VAC or 480 VAC to a control voltage of 120 VAC.
240 V Primary
Paralleling the two primary coils converts the line voltage of 240 VAC down to the desired control voltage of 120 VAC. Take a look at the diagram in Figure 6.
By connecting the primary coils in parallel, the total number of turns is equal to that of a single primary coil with 200 turns. A turns ratio of 2:1 indicates a secondary with 100 total revolutions. Therefore, a 240 VAC input will result in a 120 VAC output.
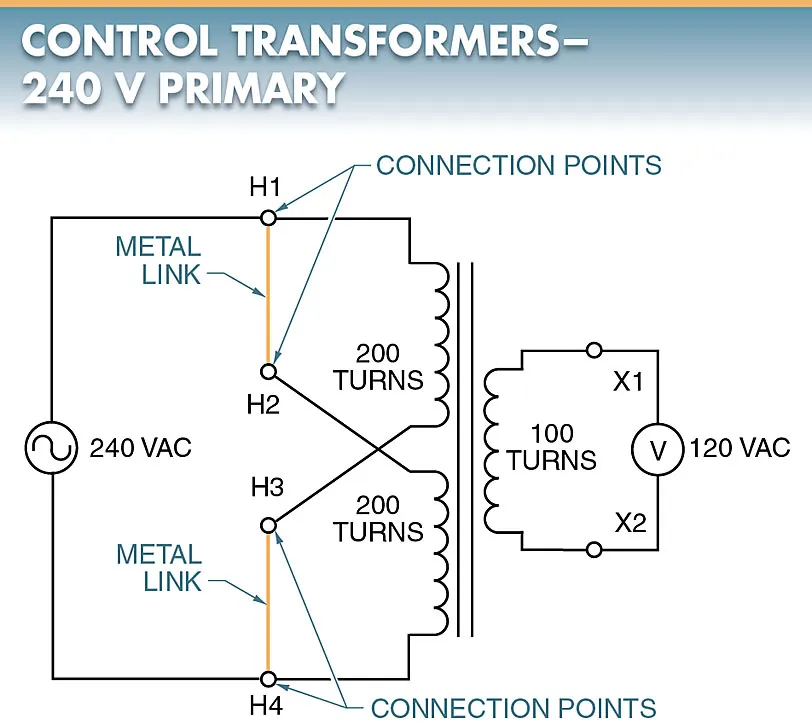
480 Volts Primary

Parallel connection of the two primary coils is required to reduce the line voltage of 480 VAC to the desired control voltage of 120 VAC. Refer to Figure 7.
Connecting the primary coils in series results in 400 effective turns, or a turns ratio of 4:1. What this means is that if you plug in a 480 VAC source, you’ll get a 120 VAC current.