An AC motor drive applies an electric load to a motor in order to slow it down at a predetermined rate. Using a motor drive to apply a braking force has the benefit of requiring very little maintenance due to the lack of moving parts that are subject to wear and tear during braking.
It is possible to use the motor drive to stop the motor and a friction brake to hold the motor shaft/load in place for applications that need to hold the load for a while after the motor has stopped. In situations where an emergency stop is necessary, friction brakes can be used in conjunction with motor drive braking.
Programmable AC motor drives allow for a variety of stopping strategies to be applied. Ramp stop, coast stop, DC brake stop, and soft stop (S-curve) are typical methods for stopping an AC motor drive. Look at the example in Figure 1.
Ramp Stop
Ramp stop is a braking method in which the level of voltage applied to a motor is reduced as the motor decelerates.
The brakes on a motor are typically set to ramp stop mode by the manufacturer. In response to a command to “stop,” the motor drive continues to regulate the voltage applied to the motor’s stator, thereby maintaining speed control. As a result, you can come to a safe and sound halt from any velocity.
The deceleration time parameter of the motor drive determines how long it takes the motor drive to stop the motor. The deceleration time can be altered from the default setting of 10 seconds to anywhere between a few seconds and several minutes. Refer to Figure 2.
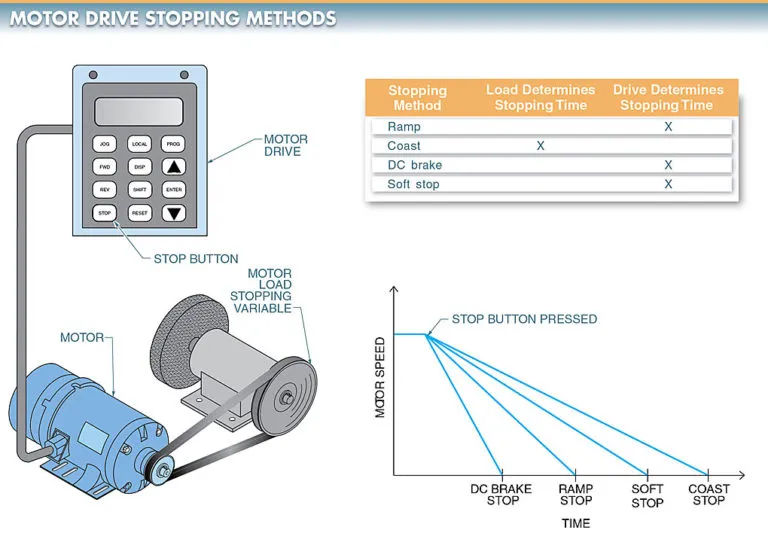
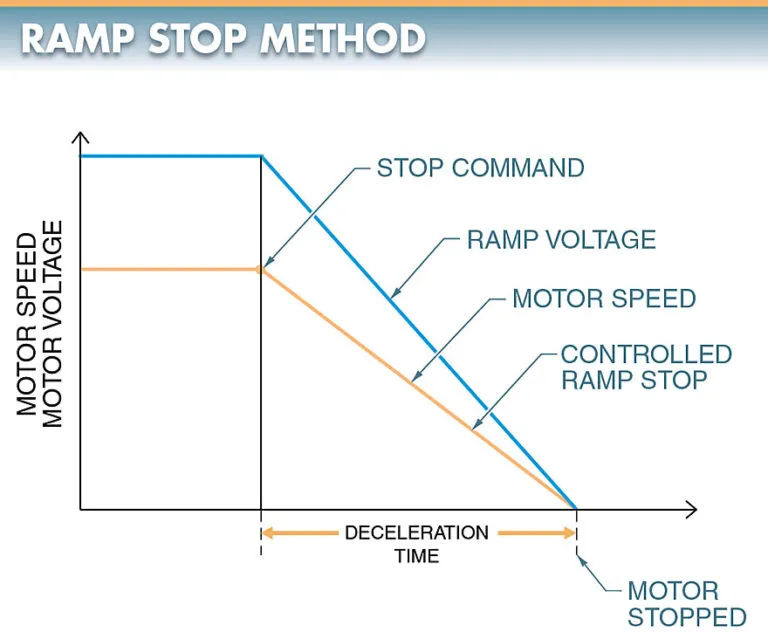
Coast Stop
Coast stop is a braking method in which the motor drive shuts off the voltage to a motor, allowing the motor to coast to a stop.
After the stop command is entered, the drive has no further interaction with the motor during a coast stop. The load on the motor affects how long it takes to come to a stop.
DC Injection Braking
DC injection braking is a braking method in which a DC voltage is applied to the stator winding of a motor after a stop command is entered.
In contrast to ramp stopping, the motor drive’s DC hold volts parameter maintains the applied DC voltage at the value set by the user. DC hold time is a parameter on the drive that controls how long the DC voltage applied to the motor stator is held constant for. Refer to Figure 3.
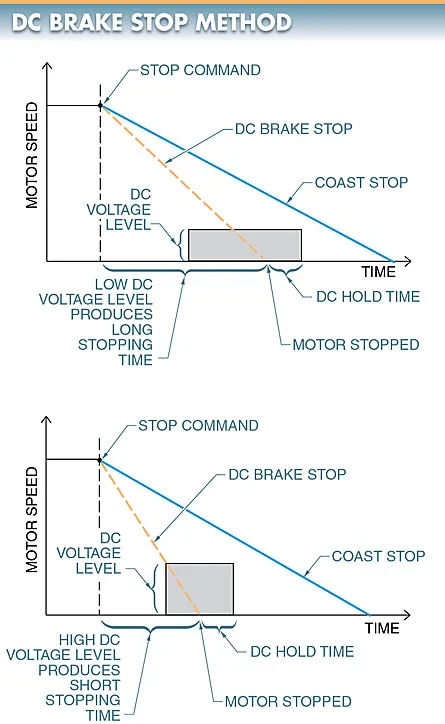
The DC injection braking method not only stops the motor quickly, but can also apply enough braking force to keep it stopped. Although effective, DC injection braking cannot replace a friction brake in situations where the motor shaft must be held for an extended period of time after the brake is applied. This is due to the fact that the maximum value for the DC hold time parameter is typically around 2 seconds. When run for too long, motor windings become dangerously hot.
Soft Stop (S-Curve)
Soft stop (S-curve) is a braking method in which the programmed deceleration time is doubled and the stop function is changed from a ramp slope to an S-curve slope.
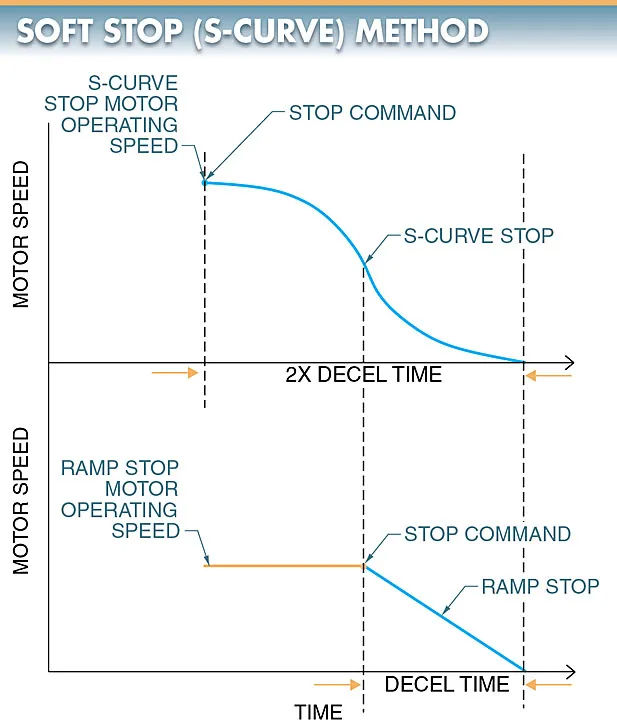
The soft stop technique allows for a gentle stopping action. Light loads (such as empty cans or bottles) may need a very soft stop to prevent them from toppling over. The motor drive can be reconfigured for soft-stop (S-curve) braking in such situations. Look at Figure 4.