Every electric motor has a nameplate that describes its capabilities and the voltage range it needs to operate.
Each motor’s nameplate must contain the information below as required by the National Electrical Manufacturers Association (NEMA):
- Duty Cycle or Time Rating
- Efficiency
- Frame size
- Frequency
- Full-Load Current (FLC — Full-Load Amps: FLA)
- Full-Load Speed
- Horsepower
- Locked Rotor Indicating Code Letter
- Manufacturer’s Name
- NEMA Design Code
- Number of Phases (for AC Motors)
- Rated Voltage
- Service Factor
- Temperature Rise or Insulation System Class
Because NEMA is a trade group rather than a government agency, not all electric motor manufacturers that meet NEMA standards are included in this list. Not all motor nameplates will have all of the NEMA-required details. Nameplates may also contain details outside of what is required by NEMA.
The information presented in this section may or may not be present on electric motor nameplates, depending on the motor’s intended use. We’ll go over everything on the nameplate in Figure 1.
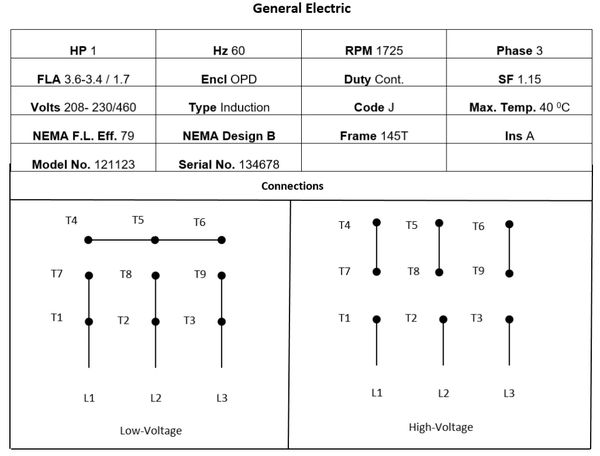
1. Horsepower Rating
Rated horsepower (HP) is a measure of an electric motor’s output power based on the maximum torque it can generate at its base speed. According to the label in Figure 1, the motor produces 1 horsepower.
The rating of steam engines is the origin of the term “horsepower.” Steam power was first introduced by James Watt, and it has been around for a long time. Horses and mules were used for transportation and labor at the time. Watt used the power output of his steam engines as a comparison to the usefulness of horses to sell his machines. Following extensive testing, he concluded that the typical workhorse possessed a work capacity of 550 foot-pounds per second (550 ft-lb/s), or 33,000 foot-pounds per minute (ft-lb/min). For the purpose of the formula;
1 HP = 33,000 ft-lb/min
James Watt also calculated that 746 watts of electricity would be required to do the work of one horsepower. With the use of a formula;
1 HP = 746 watts
2. Hertz
Hertz (Hz) is the unit of measurement for the frequency of the applied alternating current source’s sine waveform. This widespread adoption of 60 Hz is the result of the parallel grid that supports the United States’ and Canada’s utility electrical power generation, transmission, and distribution. In Europe, 50 hertz is the norm for the standard frequency of the parallel utility electrical-power grid.
The electric motor’s rotational speed is determined by two factors: the frequency of the AC source used to power the motor, and the number of magnetic poles installed in each phase of the motor. The electromagnetic field in a two-pole motor spinning at 60 hertz has a synchronous speed of 3600 revolutions per minute, measured in “pole pairs”
The rpm of a motor is measured in cycles per minute, and 3600 cycles per minute is the result of multiplying 60 cycles by 60 seconds.
When using the same method, but substituting “50 cycles/second” for “60 cycles/second,” we find that the synchronous speed of the electromagnetic field rotating about the inner face of a 2-pole electric motor operating at 50 Hz is only 3000 RPMs.
When a four-pole electric motor spins at 60 hertz, the electromagnetic field around its inner face is moving at 1800 revolutions per minute. When a 50 Hz, four-pole motor is in operation, the electromagnetic field’s synchronous speed as it rotates around the inner face is only 1500 RPM.
According to the label in Figure 1, the maximum frequency at which the motor can be run is 60 Hz. There are companies that make electric motors (AC induction motors) with a market in both the US and Europe in mind. Most commonly used electric motors will have a nameplate indicating that they can operate at either 50 or 60 hertz.
3. Revolutions per Minute
RPMs (also known as “baseline speed”) represent the maximum rotational velocity of an electric motor under rated load. When the electric motor is supplied the rated voltage specified on its nameplate and the rated frequency specified by the manufacturer, the electric motor is operating at its rated load. If supplied with 208 VAC, 230 VAC, or 460 VAC at 60 Hz, as shown in Figure 1, this specific electric motor will turn at 1725 RPMs while driving a 1 HP connected load. Both the “low-voltage” (208 or 230 VAC) and “high-voltage” (240 VAC) wiring configurations must be adhered to when using this product (460 VAC).
Since the rotor in an AC induction motor is not directly powered by the electromagnetic field as it rotates around the stator, the rotor does not turn in time with the field. The amount of “slip” between the two electromagnetic fields is the difference between the synchronous speed of 1800 RPMs (discussed above — this must be a 4-pole induction motor) and the rated speed of 1725 RPMs. As the electromagnetic field of the rotating stator circuit moves across the rotor windings, it induces a voltage on the rotor windings as a result of the slip. Shorted rotor windings conduct current due to the induced voltage. In an AC induction motor, the torque, or “motor action,” is generated by the counter-electromagnetic field created by the current flow in the rotor winding.
In addition to the synchronous speed, the torque requirement of the connected load determines the actual speed of the turning rotor. When the motor is operating with no load, the rotor’s rotational speed will be very close to that of the rotating electromagnetic field produced by the stator circuit. When the slip and delivered torque are both close to zero, the current through the stator windings are also low.
The rotor’s actual speed, the stator winding current, the amount of slip, and the delivered torque all increase from no load to full load as the torque requirements of the connected load increase.
When the connected load’s torque demands reach 1 horsepower and the motor is supplied with its rated voltage (208, 230, or 460 VAC, respectively) at 60 hertz, the rotor’s actual speed slows to 1725 revolutions per minute (the nameplate listed RPM). Depending on the voltage rating, the stator circuit will consume the FLA of current.
The mechanical overload occurs when the connected load’s torque demand exceeds 1 horsepower and the motor’s supply voltage is 208 volts, 230 volts, or 460 volts at 60 hertz. In this case, the rotor’s actual speed drops below the nameplate-rated RPM, the stator winding current rises above the nameplate FLA rating, the amount or percentage of slip rises, and the torque delivered rises. When the slowed rotor’s %-slip reaches about 20%, the AC induction motor enters breakdown torque and stops suddenly in a locked-rotor condition.
The synchronous speed is the most important factor in determining the maximum speed of a motor under full load. The motor’s construction is another important consideration. A given AC induction motor’s running and full-load speed are very sensitive to the squirrel-cage winding (configuration of the rotor bars making up the squirrel cage) in the rotor.
4. Number of Phases
Phase refers to the number of individual circuits in the power grid on which the AC induction motor is intended to run. In Figure 1, the number 3 next to the word “Phase” on the motor’s nameplate indicates that it is a three-phase AC motor and that it requires three-phase AC power. Most commercial and industrial AC induction motors require a 3-phase AC power supply, which consists of three independent but parallel single-phase AC lines, each with voltages across its windings that are 120 degrees out of phase with the others. Single- or three-phase ratings for other ac motors are possible. Single-phase alternating current (AC) induction motors find more widespread use in residential settings than in industry. It’s also worth noting that 2-phase AC induction motors do exist, but they’re hardly ever used by American businesses.
5. Full-Load Amps
When an electric motor is running at its rated load, rated voltage, and rated frequency (AC motors), the current drawn by the motor is equal to the rated-load current (RLC) listed on the motor nameplate. This is also referred to as the full-load amps (FLA), full-load current (FLC), or rated-load current (RLC) of the motor. Operating the AC induction motor without any load or with a load that is less than the horsepower rating will result in the motor drawing less current than at full load, as discussed in Section 3 in relation to the motor’s rotational speed. When the motor is subjected to a mechanical overload, it will require more power than what is specified for full load on the nameplate.
Three different full-load currents can be seen on the nameplate of the motor shown in Figure 1 because the motor is rated for three different voltages. Each voltage level gets its own. When running at full load, the 208 VAC AC induction motor’s amperage draw should be 3.6 amps if the motor’s leads are properly connected. The ac induction motor has a full load current consumption of 3.4 A at 230 VAC. The full load current draw for a 460 VAC AC induction motor should be 1.7 A. Some motor nameplates abbreviate the full-load current measurement to “AMPS” rather than the more precise “FLA,” “FLC,” or “RLC.”
6. Enclosures
Electric motors come with a variety of housing options, each tailored to a specific set of circumstances. The following are examples of common enclosures:
The cylindrical motor housing and the end bells are completely sealed off from the outside environment to make this enclosure explosion-proof (EXP) and suitable for use in potentially dangerous environments.
The most common type of enclosure is the open drip proof (ODP). There are holes in the end bells of the cylindrical motor housing to let air flow through the windings. Figure 1 shows the rating of the motor enclosure as ODP as indicated by the nameplate.
Commonly used enclosures include those with a totally enclosed fan cooling (TEFC) system. Moisture and dirt are kept out of the motor by sealing the end bells and the cylindrical housing. In order to increase the total surface area of the motor housing, fins are often molded directly onto the outer surface of the cylinder. To aid in cooling the motor, a fan is typically installed externally on a jackshaft near the end of the motor that is not used for driving.
The acronym “TENV” stands for “totally enclosed nonvented,” and it describes enclosures that can be regularly cleaned with a hose. A typical application for TENV electric motors is in industrial settings where corrosion and extreme temperatures are common, such as chemical or food processing plants.
7. Duty Cycle
According to the National Electrical Code, an electric motor’s “duty cycle” can be one of five types: continuous, intermittent, periodic, short-time, or varying. When an AC induction motor fits the bill for being labeled as
In continuous duty, the load on the motor remains relatively constant over a very long period of time. According to the designation on the motor’s faceplate (Figure 1), the duty cycle of this electric motor is constant.
This type of duty cycle is known as “intermittent duty,” and it involves the motor being on during alternating periods of (1) load and (2) no load or (3) load, no load, and rest.
In periodic duty, the motor is on and off and the load conditions occur frequently.
“Short-Time Duty” means that the motor is on for a limited amount of time and is under a constant load.
The load on the motor and the length of time it is in use can vary widely, a condition known as “varying duty.”
The duty cycle describes how often the motor should work. In the absence of evidence to the contrary, the NEC requires that “any motor application shall be considered to be for continuous duty,” meaning that a motor may be used continuously under load in any circumstance.
8. Service Factor
Overloading the electric motor by the horsepower specified by the service factor (SF) at the rated voltage and frequency is permitted under the conditions specified for the service factor on the motor’s nameplate.
Taking the nameplate horsepower rating and multiplying it by the service factor yields the maximum allowable overload. The electric motor is rated at 1 HP, as indicated on the nameplate shown in Figure 1. The 1.15 service factor indicates that the motor can handle an overload of up to 1.15 horsepower. The motor’s speed, efficiency, and operating temperature will all suffer if it’s constantly run at low loads in the service factor range. Increasing the motor’s operating temperature will not, per the rated service-factor, result in premature insulation failure.
Choosing an electric motor with a service factor greater than 1 protects the motor from intermittent heat rises and reduces the amount of excess heat generated by the variation in the single-phase AC winding currents caused by low or unbalanced line voltages, allowing the motor to be operated at rated load or less than rated load with lower winding temperatures.
For motor operations at rated voltage, frequency, and ambient temperature at sea level, the manufacturer sets the Service factor. If the intended connected load’s horsepower requirements fall between standard size horsepower ratings, it is generally preferable to install an electric motor of the next higher horsepower rating and operate it under load rather than relying on operating the motor in the service factor range to attain the required horsepower rating.
9. Voltage Rating
It is clear from the label that this is a dual-voltage AC induction motor. In electric motors, the field-terminal winding connections determine whether the motor can function satisfactorily at low voltage or high voltage. The motor can run smoothly on either 208 or 230 VAC if it is wired for low-voltage operation as shown by the terminal connections in the wiring diagram on the left side of the nameplate. If the terminal connections in the wiring diagram to the right on the nameplate are followed, the motor will function properly on 460 VAC.
10. Type of Motor
There are three distinct categories of three-phase ac motors: squirrel-cage, wound-rotor, and synchronous. Induction motors can have either a squirrel-cage rotor or a wound rotor. In an induction motor, the rotor circuit does not require an external power source, as was explained in Section 3, RPM. When current is passed through the stator windings, the revolving electromagnetic field induces a voltage in the rotor windings.
The term “squirrel-cage” refers to the rotor design of most ac motors; these rotors have bars that resemble a squirrel cage or the paddle wheel of a steamship and are typically cast in aluminum (Figure 2).
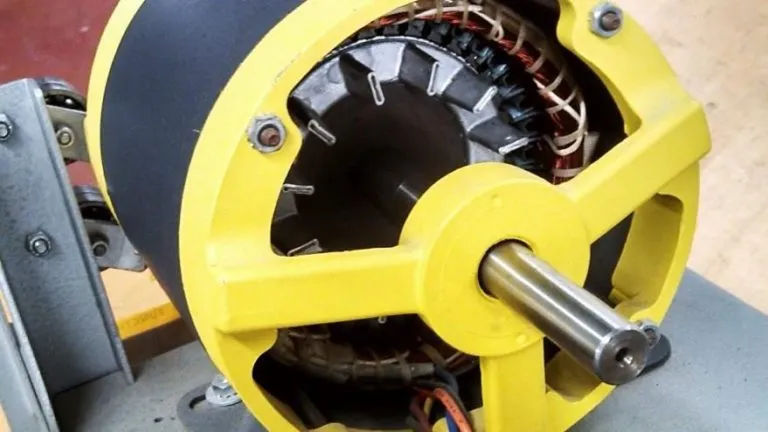
To illustrate, the rotor bars of an AC induction motor with a squirrel-cage rotor are cast from aluminum and have the appearance of a squirrel cage or the paddle wheel of a steamship (see Figure 2).
All you need to do is look for the three slip rings on the rotor shaft of a wound-rotor induction motor (Figure 3). The wound-rotor differs from the squirrel-cage rotor in that it uses a steel frame to hold the windings of insulated wire. The three single-phase windings are connected in a wye fashion at one end, with the other ends going to the respective slip rings.
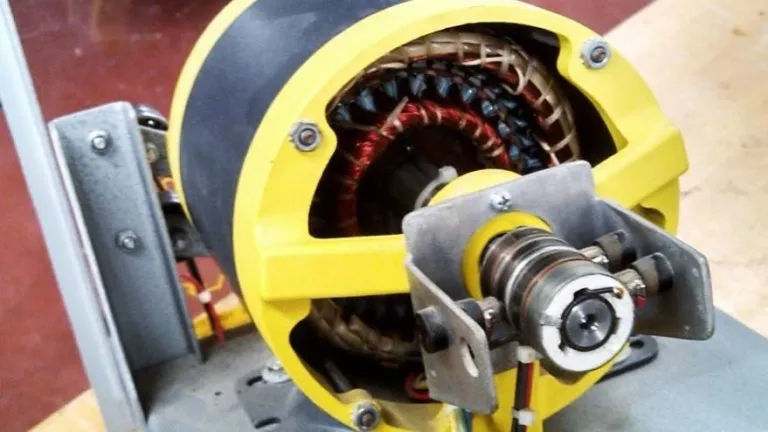
If you look closely at the rotor shaft of an AC induction motor, you’ll notice three slip rings, as shown in Figure 3.
The magnitude of the rotor current is regulated by a 3-phase or “3-leg” wye-connected resistive load bank, with brushes riding on the slip rings. However, the 3-phase resistive load bank is typically used to reduce the impact of the starting torque of the induction motor, and the individual resistors in the load bank are bypassed or shorted in three or four successive steps until all the resistance is removed from the rotor circuit, allowing for some speed control of the wound-rotor motor.
Slip rings on the rotor shaft are a telltale sign of a synchronous motor. Although synchronous motors evolved from induction motors by employing an amortisseur winding on the rotor assembly, they do not belong to the family of AC motors known as inductors.
The rotor assembly of an AC synchronous motor features an electromagnet in addition to the amortisseur winding. DC power is applied to the electromagnet’s winding through the two slip rings and the motor is started. The rotor assembly now rotates at synchronous speed, with no slip, because the electromagnet’s magnetic poles have locked in or with the opposite poles of the stator assembly’s rotating magnetic field.
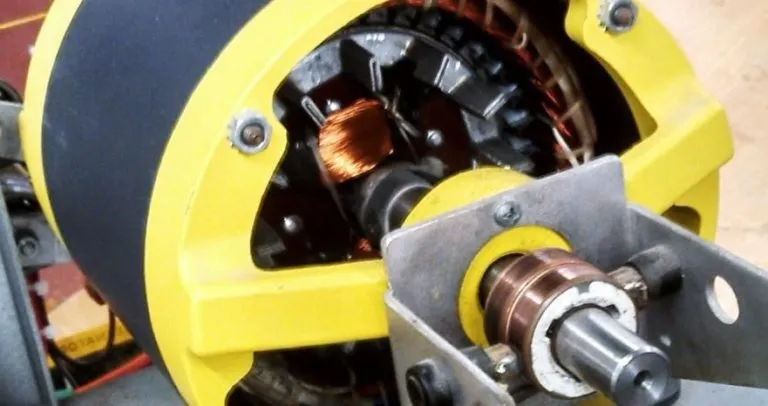
Diagram of AC The rotor shaft of a synchronous motor has two slip rings.
11. Code Letter
The AC induction motor’s nameplate will indicate whether the motor has a squirrel-cage rotor by a code letter (A, B, C, D, E, F, G, H, J, K, L, M, N, P, R, S, T, U, or V) based on the rotor’s construction. By multiplying the locked-rotor code letter by the kVA values from the National Electric Code, one can get a rough estimate of the amount of inrush current that will be drawn from the power supply when the motor is started under load. Figure 1 is a label from the AC induction motor, which specifies that it has a type J rotor. According to the NEC, the kilovolt-ampere rating for a type J rotor at locked rotor can be anywhere from 7.1% to 8% of the rated rated rated rated kVA. The inrush current range of this motor can be calculated using the 3-phase AC power formula, solved for current, assuming the motor will run on 208 volts and one horsepower.
Low-Side Locked-Rotor Amps: [1000 (/k) x 7.1 kVA/HP x 1 HP] ÷ (1.732 x 208 volts) = 19.7 amps
High-Side Locked-Rotor Amps: [1000 (/k) x 7.99 kVA/HP x 1 HP] ÷ (1.732 x 208 volts) = 22.2 amps
Starting current for the AC induction motor identified by this electric-motor label should be between 19.7 and 22.2 amps.
12. Maximum Temperature
The maximum temperature listed on the motor’s nameplate is the maximum increase in ambient temperature that can be expected from the electric motor under continuous full load operation. According to the label in Figure 1, the motor can get no hotter than 400 degrees Celsius.
13. Motor Efficiency
The overall efficiency of an AC induction motor can be gauged from its NEMA full-load efficiency rating. According to the label in Figure 1, this motor has a 79% efficiency. The percentage of the electrical energy fed into the electric motor that is transformed into kinetic energy is listed in the NEMA full-load efficiency. The rest of the power is wasted, and it gets turned into heat.
14. NEMA Design Letters
Depending on how they were built, induction motors can have wildly different operational characteristics. The operating characteristics of an ac induction motor are determined by several factors, including the amount of iron used in the stator assembly, the wire size and the number of turns of wire in the stator windings, and the rotor design (the type of squirrel-cage rotor).
Recently, NEMA assigned code letters to general purpose motors based on operating characteristics like starting current, % of slip, breakdown torque, and locked rotor torque in an effort to standardize the performance of ac induction motors. These are the NEMA letters: A, B, C, and D.
In general, Design A AC induction motors have a normal starting torque but a high starting current. Motors with a Design A are able to withstand momentary, extreme loads.
The most common type of AC induction motor has a design code of “B,” which stands for “B” design. Starting current is low for these motors, but they still produce a normal amount of torque at startup. The lock rotor starting torque of Design B motors is high enough to start the vast majority of industrial loads. According to its identification plate (Figure 1), this is a NEMA Design B motor.
A design C AC induction motor has a high starting torque at a relatively low starting current. Design C motors, which are used to start heavy loads, display a lot of rotor slip when the load is applied.
Pattern D AC induction motors with the letter D design code, like Design C motors, have high starting torques with low starting currents. Rotor slip is very noticeable in Design D motors when a load is applied, as is the case with all other designs.
Many electric motors will have a code letter (Section 11, Code Letter) that indicates whether or not the rotor is locked.
15. Frame Sizes
The motor’s make and size are denoted by the frame number on the label. According to the label in Figure 1, this electric motor has a 145T frame.
Electric motor frame dimensions are typically found by consulting a manufacturer’s chart. Motor specifications are typically listed on a manufacturer’s chart, which includes dimensions like shaft height above the bottom of the base, distance from the center hole on the front of the motor base mount to the center of the shaft, motor height, and motor width minus the terminal connection box.
With regards to frame sizes, a good rule of thumb is that the centerline shaft height above the bottom of the base in inches is equal to the first two digits of the frame number divided by 4. According to Figure 1, a frame 145T has a shaft height of 3.5 inches (14 divided by 4), which is slightly above the motor’s mounting base.
Different types of frames are indicated by both numbers and letters appended to the numbers. The alphabet consists of the following letters: C, D, H, J, JM, JP, S, T, U, Y, and Z.
C A flange-mounted electric motor is indicated by the letter C in the suffix. Flange-mounted motors typically come in the C frame design. The motor can be mounted directly to the device it is powering thanks to the threaded bolt hole pattern on the motor’s face (the end of the shaft).
D Similarly, an electric motor with the letter “D” as a suffix is a flanged design. D frame motors have a larger flange diameter compared to the motor itself. Bolts can simply slide through the holes; they are not threaded.
H When attached to certain 55-frame electric motors, the letter H at the end of the part number denotes that the frames can be mounted in either the 56-, 743T-, or 745T-position at the base.
J The letter “J” at the end of the model number denotes that the motor can be easily attached to jet pumps. A J frame motor has a 56C face and a threaded stainless steel shaft.
JM The initials JM after a jet pump’s model number denote that its shaft was manufactured with a mechanical seal in mind. The 56C face can also be found on an electric motor with a JM frame.
JP The letters JP after a jet pump’s model number denote that the pump’s shaft is built to accommodate a packing-type mechanical seal.
S A direct-coupled electric motor with a short shaft is denoted by the letter S as a suffix. Electric motors of this type are not designed to be used with belt drives.
T conforms to NEMA standards As of 1964, the T-frame engines. If the frame size of your electric motor ends in a “T,” then it was made after 1964.
U In 1952, NEMA established its first set of motor frame standards. From 1952 to 1964, the United States produced electric motors with the letter U appended to the end of the frame size number.
Y If the frame number ends in a “Y,” then the electric motor has a unique mounting arrangement. Only that the mounting configuration is nonstandard is communicated by the letter Y as a suffix.
Z The letter Z at the end of the model number designates a motor with a unique shaft. It’s possible that the shaft will be non-standard in length or diameter. It might have threading or holes. The letter Z in the motor’s frame number doesn’t mean anything other than that the shaft is unique in some way.
16. Insulation Temperature Rating
Lifespan of an electric motor is significantly impacted by insulation type, which in turn is determined by the operating temperature rating of the winding insulation. When a motor is running at full load, the temperature at its hottest point along the inner surfaces of the motor assembly/enclosure is used as an indicator of the motor’s operating temperature. In order to establish an appropriate operating temperature for a motor, both the motor’s internal temperature and the ambient air temperature must be known. In order to function properly, electric motors used in warmer regions, such as those located near the equator, require insulation with a higher temperature rating than those used in colder regions, such as those located between the United States and Canada.
Insulation can be classified as “Class A,” “Class B,” “Class F,” or “Class H” based on its thermal capacity. Those numbers and letters denote the highest allowable temperatures for each insulation type over a 20,000-hour period with the electric motor operating at full load. The motor has a Class A insulation temperature rating, as indicated by the nameplate in Figure 1.
Class A insulations can be used safely up to a temperature of 1050C, the lowest of the four classifications. Class H insulations can withstand temperatures up to 1800C, making them the safest to use. Class B insulations have an operating temperature rating of 1300C, while Class F insulations have an operating temperature rating of 1550C.
17. Model Number
The manufacturer assigns a model number to every electric motor they produce, including AC induction motors, which are typically used to purchase a replacement motor with the same ratings and operating characteristics. In Figure 1 we can see the identification plate bearing the model number 121123, which identifies the motor.
18 Serial Number
Each electric motor has a unique serial number that was also given to it by the manufacturer. There shouldn’t be any other electric motors on the market with the same serial number. The model number is used to identify the specific type of electric motor being covered by the warranty, while the serial number is used to distinguish this motor from all other electric motors in the plant or elsewhere in the manufacturing facility. See Figure 1 for the identification plate showing that the motor’s serial number is 134678.