Induction with three separate phases Reversing the direction of a motor simply requires switching two of the three lines supplying power to the motor. Line 1 and 3 are typically switched as it is the norm. For motors that need to be operated both clockwise and counterclockwise, a reverse starter is required.
Reverse Starter
Overload protection is built into one of the contactor poles of a two- or three-pole reverse starter.
In addition to the open seal-in contacts, both contactors need a set of normally closed auxiliary contacts. As a means of locking components together, normally closed contacts will be implemented. The secondary interlocking coil is connected in series with the primary coil. If the coils of the starters are wired through the opposite auxiliary normally closed contacts, there is no way for both coils to be energized at once, which is a potentially deadly scenario even if the wiring is done incorrectly.
In order to prevent the coils from being pressed in simultaneously, most reversing starters feature a mechanical interlocking device. Starter coils are manually engaged with screwdrivers by many service technicians. This troubleshooting strategy is illegal because it involves taking unnecessary risks.
Pushbutton Interlocking
Push-button interlocking is yet another option for securing doors and other mechanisms. The control technician may use pushbutton or button interlocking as a form of control wiring. There are three buttons on the panel. Two of the buttons, labeled “make” and “break,” have normally open contacts while the third, labeled “stop,” has a normally closed contact.
The motor can be started in “forward” or “reversing” rotation thanks to the buttons’ dual-direction wiring. By pressing the opposite rotation pushbutton, the power to the energized coil is cut off at the seal-in contact, allowing the load to spin in the opposite direction. To activate the non-running coil, press the button while both contactors are de-energized.
Both coils can be safely de-energized before the other coil is started thanks to a built-in interruption of the control circuit. All three forms of interlocking must be put into place for maximum protection of workers and machinery.
Reversing Starter Operation
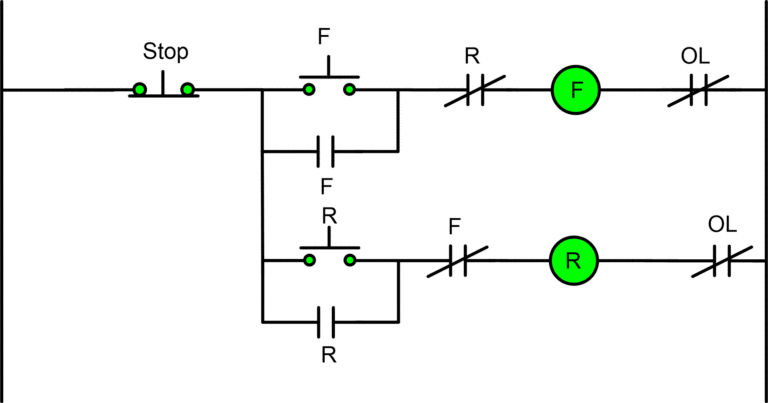
In configuration 1, the Reversing Starter functions as follows:
- Forward and reverse pushbuttons activate contactors that set the motor in motion in the respective directions.
- Power will be sent to the coil via the reverse auxiliary contact if the forward pushbutton is pressed.
- The forward normally open seal-in contact will supply power to the coil.
- Since the forward auxiliary contact is currently open, the reverse pushbutton is disconnected from the circuit and the reverse contactor cannot be energized while the forward contactor is operating.
- When the forward motor starter’s normally open seal-in contact is pressed, power is released, allowing the reverse pushbutton to be pressed and the motor to be turned in the opposite direction.